Mar
15
Optomech Pharmaceutical Cap Inspection
Pharmaceutical Cap Inspection
Why Pharmaceutical Cap Inspection is Critical
In pharmaceutical manufacturing, pharmaceutical cap inspection is as crucial as the product itself. A bottle’s cap or closure plays a vital role in maintaining sterility, preventing contamination, and ensuring patient safety. Even small flaws in caps—such as improper sealing, contamination, or damage—can lead to severe consequences, including product recalls, regulatory non-compliance, and financial losses. Automated cap inspection is essential to guarantee product safety and meet global pharmaceutical standards (FDA, WHO, GMP, ISO 9001). The Optomech CIS-XL Closure Inspection System, along with other machine vision inspection technologies, offers 100% inline, high-speed quality control, eliminating human error and improving productivity.
Common Defects in Pharmaceutical Cap Inspection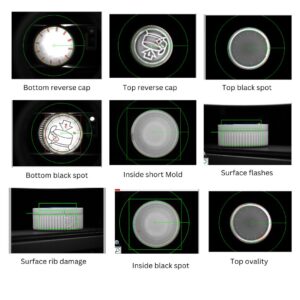
Short Molding
Occurs when the plastic fails to fill the mold completely. This leads to fragile caps that could break or malfunction during sealing.
Flashes and Extra Material
Molding errors result in excessive plastic around the edges, altering the cap’s fit and potentially causing sealing issues.
Black Spots and Contamination
Burned plastic or foreign particles embedded in the cap material could contaminate the medication.
Thread Damage
Faulty or insufficient cap threads hinder proper closure, leading to issues like leakage, sterility loss, or sealing failure.
Diameter and Ovality Variations
Dimensional irregularities can cause caps to fit too loosely or too tightly, affecting the capping process and sealing integrity.
Height Variations
Misaligned caps due to height inconsistencies can lead to rejection by filling machines and inconsistent sealing.
Cracked Caps
Caps may break due to weak molding or mechanical stress during storage or transportation.
Because of these defects, automated vision inspection systems are indispensable in high-speed pharmaceutical production. They reduce rejection rates, minimize waste, and enhance overall productivity.
Manual vs. Automated Cap Inspection: Why Machine Vision is the Future
Manual Inspection: The Limitations
Human Error: Fatigue, inconsistency, and subjective judgment can affect accuracy.
Slow & Inefficient: Manual inspection is not scalable for high-speed production.
High Labor Costs: Large QC teams are necessary to inspect thousands of caps.
Regulatory Risks: Limited traceability makes audits and compliance more difficult.
Automated Cap Inspection: The Advantages
✅ 100% Inspection at High Speeds: Inspecting 14,000 caps per hour with the CIS-XL.
✅ Eliminates Human Error: Instantaneous and reliable defect detection.
✅ Cost-Effective: Reduces production waste and lowers labor expenses.
✅ Regulatory Compliance: Ensures conformity with FDA, GMP, and ISO 9001 standards.
✅ Data Logging & Reporting: Custom reports simplify audits and ensure traceability.
With advanced AI-based image processing and high-speed cameras, the Optomech CIS-XL ensures pharmaceutical manufacturers achieve unparalleled quality control.
How the Optomech CIS-XL Cap Inspection System Works
High-Speed Image Capture
Multiple machine vision cameras capture 360° views of caps. The images are analyzed in real-time to detect defects.
Advanced Lighting for Precision Detection
Customized LED lighting highlights imperfections, ensuring high-contrast defect detection with backlighting and side illumination.
AI-Based Image Processing
Machine learning algorithms detect and classify defects, while an automated rejection system eliminates defective caps.
Integration with Production Lines
The CIS-XL seamlessly integrates with existing high-speed capping lines, conveyors, and ejection systems.
Real-Time Monitoring & Reporting
Predictive maintenance insights help optimize quality control, with custom reports ensuring audit and compliance traceability.
Key Features of the Optomech CIS-XL Closure Inspection System
High-Speed Inspection: Inspect 14,000 caps per hour.
11 Vision Cameras: Capture defects from various angles.
Customizable Tolerances: Set acceptance and rejection criteria based on your needs.
Automated Sorting & Rejection: Defective caps are automatically removed through a pneumatic system.
Remote Monitoring: Access diagnostic reports and real-time data online.
GMP & FDA Compliance: Fully validated system meeting 21 CFR Part 11 standards.
Regulatory Compliance and Industry Standards
To meet pharmaceutical industry standards, cap inspection systems must comply with:
FDA 21 CFR Part 11: Ensures data integrity and audit trails.
GMP (Good Manufacturing Practices): Ensures the safety of pharmaceutical products.
ISO 9001: Standardizes quality management systems.
WHO & EU GMP Guidelines: Global standards for pharmaceutical safety.
The Optomech CIS-XL complies with these stringent regulations, helping manufacturers avoid compliance issues and costly recalls.
Case Study: How Automated Cap Inspection Prevented a Product Recall
A major pharmaceutical company faced significant challenges with unreliable capping, resulting in:
A 5% production fault rate.
Shipment delays due to quality control bottlenecks.
The potential for FDA regulatory action.
Solution: Implementing CIS-XL
✅ The system was seamlessly integrated into the production line.
✅ Cap defects were reduced to 0.2% within the first month.
✅ Labor costs for manual quality control were cut, saving $200,000 annually.
✅ The company ensured full compliance with FDA and GMP regulations.
Challenges in Implementing a Pharmaceutical Cap Inspection
Initial Investment: While high-quality vision systems require a capital investment, the savings in labor costs and defect reduction lead to a quick return on investment.
Integration Complexity: The Optomech CIS-XL easily integrates with existing conveyor systems.
Operator Training: With its intuitive touchscreen interface, operator training is straightforward.
Future Trends in Pharmaceutical Cap Inspection
AI-Powered Defect Recognition: Self-learning systems enhance defect detection.
Predictive Maintenance: IoT sensors help prevent machine downtime.
Industry 4.0 and Smart Factories: Data exchange enables global quality control networks.
More Compact, Faster Machines: Future systems will have smaller footprints and increased speeds.
Conclusion: Why Invest in an Advanced Cap Inspection System?
Automated cap inspection is now a necessity for pharmaceutical companies to meet:
Strict GMP and FDA regulations.
Demands for high-speed, high-accuracy production.
The need for defect-free product quality.
Cost savings from reduced defects and labor expenses.
The Optomech CIS-XL Closure Inspection System stands out as the ideal solution for inspecting pharmaceutical caps, providing unparalleled accuracy, speed, and regulatory compliance.