Mar
18
Desiccant Canister Inspection
Desiccant Canister Inspection System
Introduction: Why Desiccant Canister Inspection is Essential
Desiccant Canister Inspection in pharmaceutical packaging, silica desiccant canisters play a crucial role in preserving the stability and efficacy of moisture-sensitive medicines. These small canisters are inserted into tablet containers to absorb excess moisture and prevent degradation of pharmaceutical products.
For desiccant canister manufacturers, maintaining high-quality production standards is critical because:
✅ Pharmaceutical companies demand zero-defect packaging to meet FDA, WHO, and GMP standards.
✅ Defective canisters with structural flaws or contamination compromise drug stability.
✅ Manual inspection is inefficient and fails to catch micro-defects at high production speeds.
To eliminate defects and ensure 100% quality control, automated desiccant canister inspection systems are now a must-have for canister manufacturers.
Common Defects in Silica Desiccant Canisters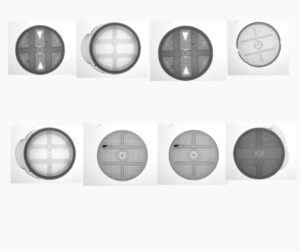
- Structural Defects
- Short Molding – Incomplete material filling, leading to weak canisters.
- Flashes & Extra Material – Excess plastic affecting canister fitment.
- Corner Breakage – Canisters cracking at stress points.
- Diameter & Height Variations – Dimensional inconsistencies affecting container compatibility.
- Mesh & Airflow Defects
- Broken Mesh – Impairs moisture absorption efficiency.
- Blocked Holes – Restricts airflow, reducing desiccant performance.
- Contamination & Visual Defects
- Black Spots & Material Inclusions – Foreign particles in the plastic.
- Surface Contamination – Dust or oil residues impacting pharmaceutical compliance.
- Discoloration & Burn Spots – Indicate overheating during production.
- Shape & Dimensional Variations
- Ovality – Canisters that are not perfectly round, affecting proper sealing.
- Incomplete Blowing – Undersized or deformed canisters.
Defects in desiccant canisters can lead to moisture control failures, resulting in drug spoilage, compliance violations, and costly recalls.
Challenges of Manual Inspection vs. Automated Inspection
Manual Inspection: Why It’s No Longer Sufficient
Human Error – Fatigue and inconsistency lead to missed defects.
Slow & Inefficient – Cannot match high-speed production demands.
High Risk of Recalls – Undetected defects cause product failures.
Regulatory Compliance Issues – Manual inspection lacks traceability and accuracy.
Automated Vision Inspection: The Best Solution
✅ 100% High-Speed Inspection – Optomech CANIS inspects 14,000 canisters per hour.
✅ Eliminates Human Error – Consistently detects all defects.
✅ Automated Rejection – Defective canisters are immediately removed.
✅ Meets Regulatory Standards – Ensures GMP, FDA, and ISO 9001 compliance.
How the Optomech CANIS Desiccant Canister Inspection System Works
- High-Speed Image Capture
- Uses multiple vision cameras to inspect all surfaces of the canister.
- Detects shape defects, contamination, and airflow obstructions.
- Precision Lighting for Accurate Detection
- Customized lighting technology highlights even the smallest structural flaws and surface defects.
- AI-Based Image Processing
- AI and deep learning algorithms process images in real time to detect defects.
- Instant pass/fail decision ensures 100% inline quality control.
- Automated Sorting & Rejection
- Defective canisters are immediately ejected, preventing contamination in the packaging line.
- Reporting & Compliance Tracking
- Detailed batch reports allow manufacturers to track defect trends and improve process efficiency.
- Meets pharma audit requirements with secure data logging.
Key Features of the Optomech CANIS Canister Inspection System
High-Speed Inspection – 14,000 canisters per hour.
Multi-Camera Vision System – Captures defects from multiple angles.
Customizable Inspection Parameters – Set acceptance/rejection tolerances.
Automated Defect Sorting – No manual handling required.
Remote Monitoring & Troubleshooting – Access real-time system diagnostics.
GMP & FDA Compliance – Ensures regulatory adherence for pharmaceutical packaging.
Regulatory Compliance & Industry Standards
Pharmaceutical packaging components, including desiccant canisters, must comply with:
✔ FDA 21 CFR Part 11 – Ensures audit trails and data integrity.
✔ GMP (Good Manufacturing Practices) – Requires 100% defect-free canisters.
✔ ISO 9001 – Standardized quality management processes.
✔ WHO & EU GMP Guidelines – Global pharmaceutical safety compliance.
The Optomech CANIS system ensures full regulatory compliance, helping desiccant canister manufacturers avoid compliance risks and product failures.
Case Study: How Automated Inspection Reduced Defect Rates by 95%
A leading silica desiccant canister manufacturer faced:
High rejection rates (8-10%) due to defects.
Manual QC inefficiencies, leading to shipment delays.
Failed pharmaceutical audits due to quality inconsistencies.
Solution: Implementing Optomech CANIS
✅ Reduced defect rates to 0.5% within the first 2 months.
✅ Eliminated manual inspection, saving $200,000 annually.
✅ Achieved 100% compliance with pharmaceutical industry regulations.
Challenges in Implementing a Canister Inspection System
Initial Investment – High-quality vision systems require capital investment but deliver rapid ROI.
Integration Complexity – The CANIS system is designed for seamless integration with production lines.
Operator Training – User-friendly touchscreen interface ensures ease of use.
Future Trends in Desiccant Canister Inspection
AI-Powered Defect Recognition – Self-learning algorithms enhance detection accuracy.
Predictive Maintenance – Sensors detect machine wear to prevent failures.
Industry 4.0 & IoT Integration – Real-time quality data sharing for global monitoring.
Compact, High-Speed Machines – Higher efficiency with smaller machine footprints.
Conclusion: Why Invest in a Desiccant Canister Inspection System?
For desiccant canister manufacturers, investing in automated inspection is essential to:
✅ Deliver defect-free canisters to pharmaceutical customers.
✅ Ensure GMP, FDA, and ISO 9001 compliance.
✅ Reduce quality control costs and minimize waste.
✅ Improve production efficiency and business reputation.
Want to ensure flawless desiccant canister quality? Contact us today for a demo of the CANIS system!